Case Study | Securing Steel Coils in Shipping Containers
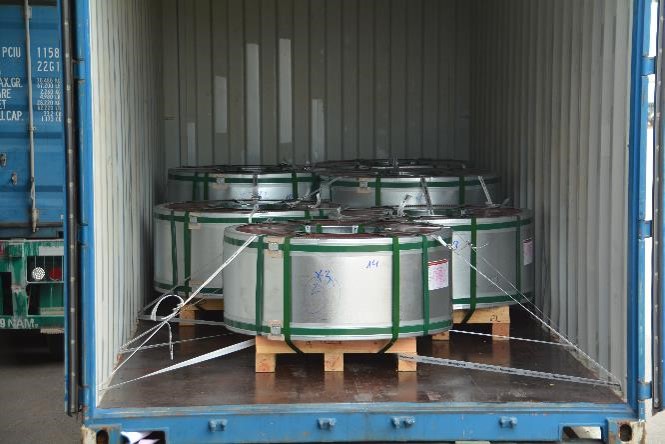
Cordstrap container solution results in:
- increased container output of 330%
- cost savings consumables 50% per container
For a large global manufacturer and exporter of steel, Cordstrap was asked to provide a more cost- and time efficient solution for securing steel coils in shipping containers, in compliance with the CTU Code. Currently the company was using a combination of steel strapping and wire rope.
Current situation
Currently the company was using steel strapping and wire rope. This method involved a lot of prep time, warehouse space, expensive consumables and too much manpower.
To secure the load in each container involved 8 workers and took 2 hours. This allowed them to secure only a maximum of 15 containers per day.
The night prior to loading, the lashing team had to prepare wire rope arrangements, cut steel strapping to the required length and prepare wood chocking. This required much needed warehouse space, including a woodworking station to cut wood and a forklift to move the steel strap and wire rope. As the photos show, the prep work also resulted in shocking amounts of waste and disposal.
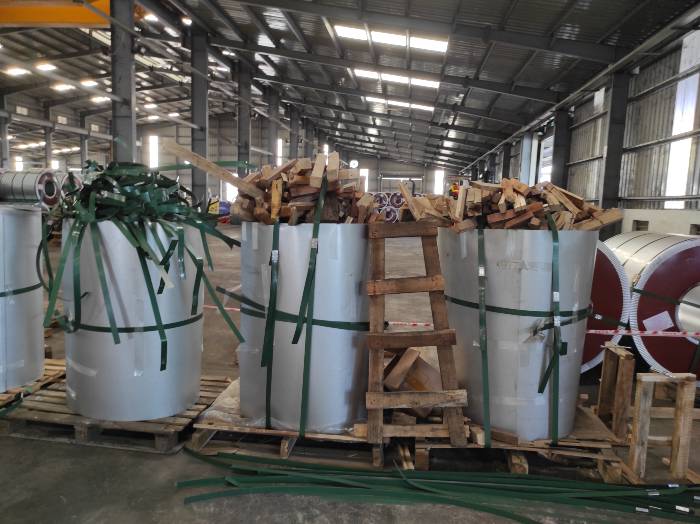
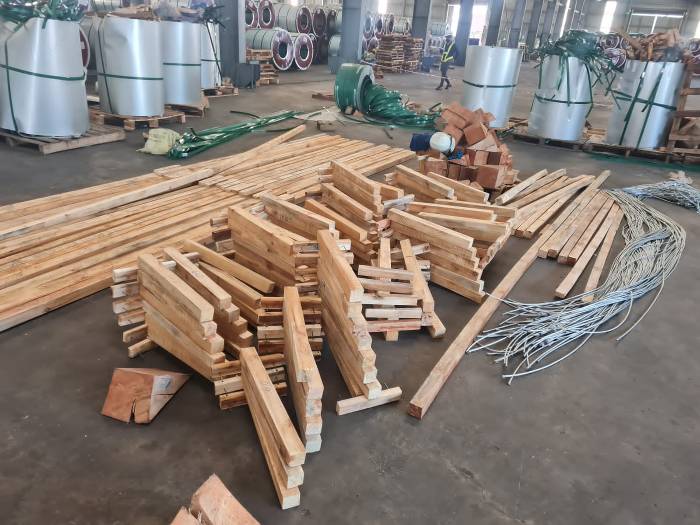
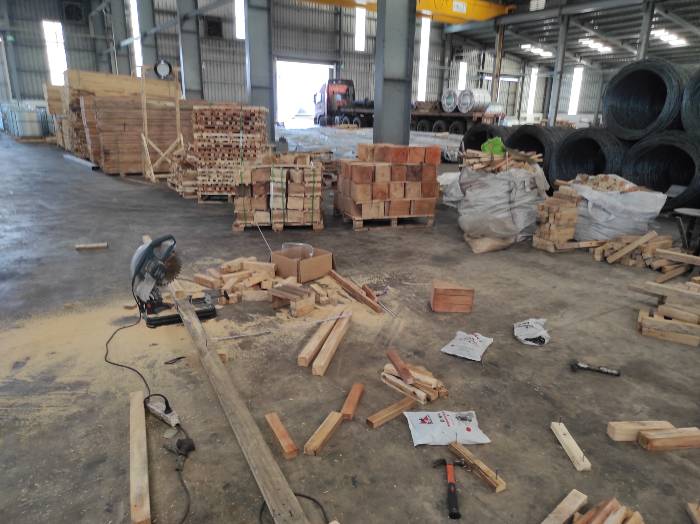
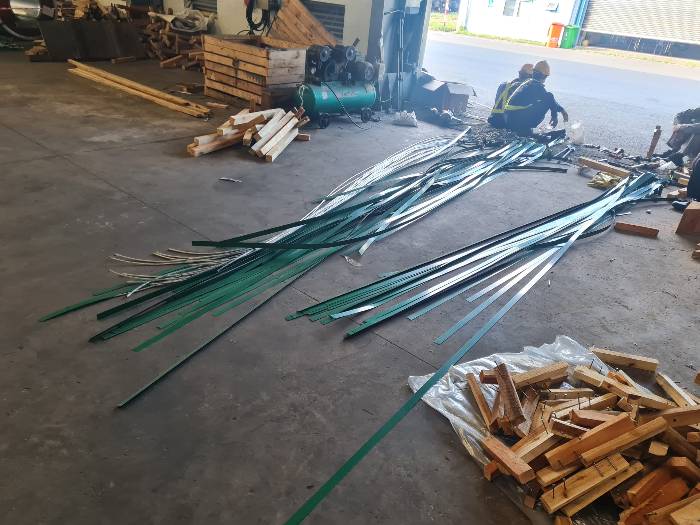
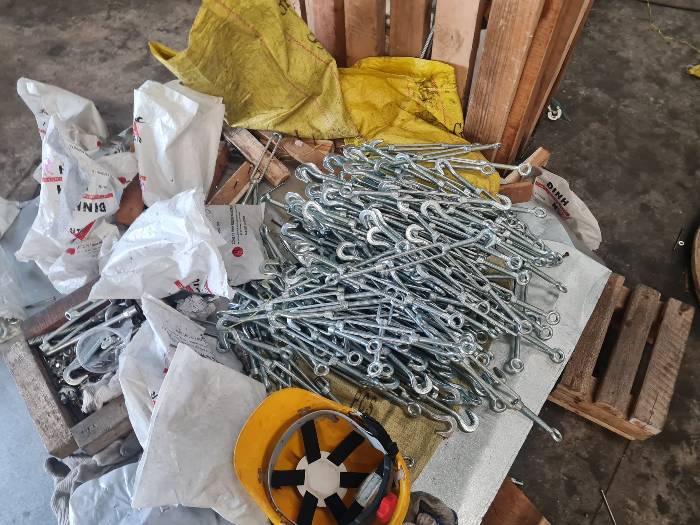
The Trial with Cordstrap
Below are the details of the load and the steps we took to secure this load.
Load Details
- Material to secure: steel coils
- Total units: 6
- Gross weight : 22.097kg
- Mode of transport: CTU Container 20ft
Step 1 – Unitising the coils
The first step after loading the steel coils is to unitising the coils. For this we used Cordstrap 32mm composite lashing and 32mm Cordstrap Wire Buckles. The system strength of this system is 2,600kg.
- Quantity composite lashing used for unitising all coils: 20 meters
- Quantity buckles used for unitising all coils: 8 pieces
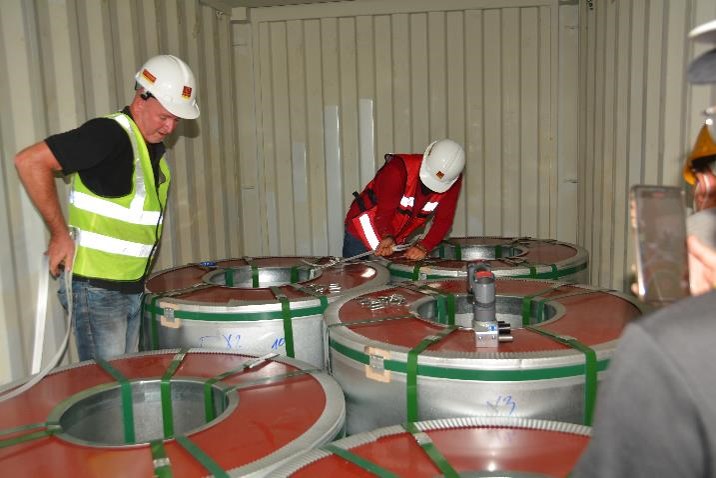
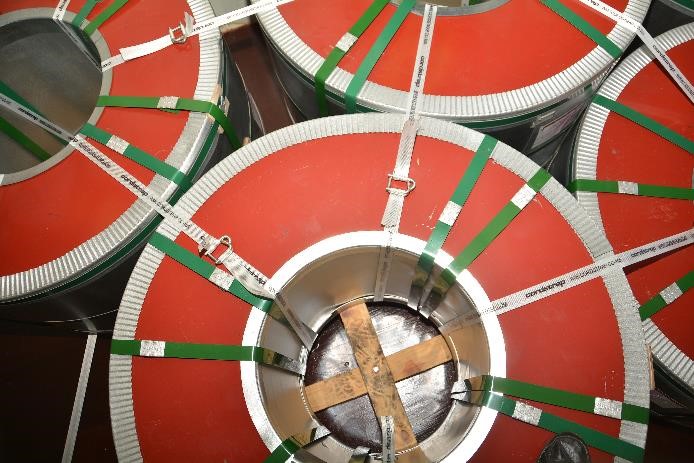
Step 2 – Lashing the coils
After unitising the coils, it was time to secure the unitised coils to the shipping container. For this we also used Cordstrap 32mm composite lashing and 32mm Cordstrap wire buckles. The system strength of this system is 2,600kg.
- Quantity composite lashing used for lashing all coils: 50 meters
- Quantity buckles used for lashing all coils: 10 pieces
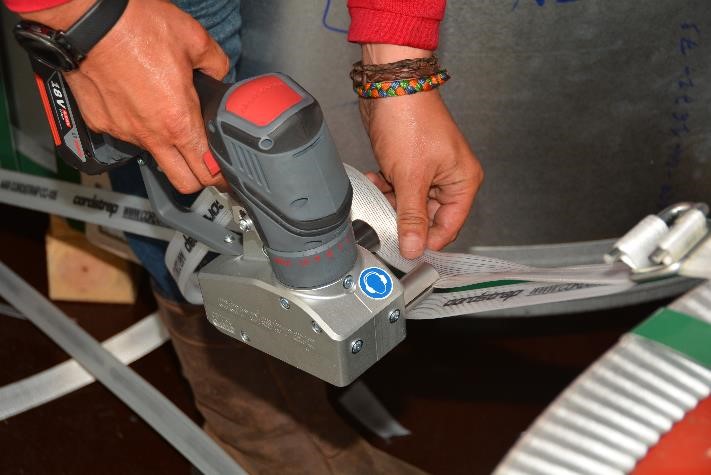
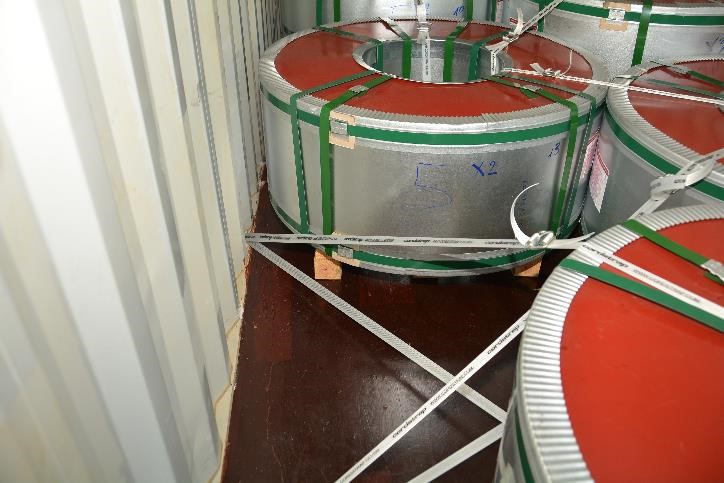
Total time and manpower used
- 2 workers
- No prep time
- Total time spend: 35 minutes
Total amount consumables used
- 70 meters Cordstrap composite lashing (CC-105 – 32mm 2,600kg system breaking strength)
- 18 Cordstrap buckles (CB-10)
Total cost of consumables used was less than AUD$50
To tension the system a tensioner is required. We offer manual, battery and pneumatic tensioners. For this trail the Cordstrap Battery Tensioner CBT-35 was used.
Benefits of the Cordstrap vs Steel Strap / Wire Rope
- Safe, for user and receiver
- Time & Cost Efficient (Easy and quick to install; only 1 tool needed. Choice of manual, battery or pneumatic tools)
- DNV/GL Certified, CTU Code Compliant & AAR approved lashing system
- Lots of flexibility to move around in tight container spaces as you decide where to place the buckle to close and tension the system.
- Only use the length you need, no waste.
- No need to pre-cut the straps
- Easy to dispose off at arrival
Summary
Current Method
- 8 workers
- 2 hours per container
- 15 containers per day
- warehouse space needed for prep work
- forklift needed to move steel straps
- wood working station to cut timber
- massive amount of waste/disposal
Prep work
- prepare wire rope arrangements
- pre-cut steel straps to size
- prepare timber chocking
Cordstrap Method
- 2 workers
- 35 minutes per container
- 50 containers per day
- no requirement for warehouse space
- no requirement for forklift
- no requirement for wood working station
- no waste
Prep work
No prep work involved
Feedback
Besides the increased container output of 330% and an estimated cost-savings of 50% in consumables per container, the company was extremely pleased with the reduced worker fatigue doe to heavy tools and material and long hours in hot and humid conditions.
The customers of the company were extremely pleased. The load was well secured upon arrival. Removal, or cutting of the lashing, was safe, quick and easy. The disposal of the lashing and buckles was easy and waste was only a fraction of steel strapping and wire rope.